This futuristic recycling plant is mining your old phone for gold
Camden Wrather’s Carlsbad, California, recycling facility shreds old circuit boards—and has a far lower carbon footprint than other methods.
If you drop off an old cell phone for recycling, the circuit board inside it will probably be taken out, packed in a crate, and shipped off to a smelter in Europe or Asia who heats it up to more than 1,800 degrees Fahrenheit to melt down the valuable metals it contains. Then the melted metal goes to a refiner. The process works, but it also has a huge carbon footprint.
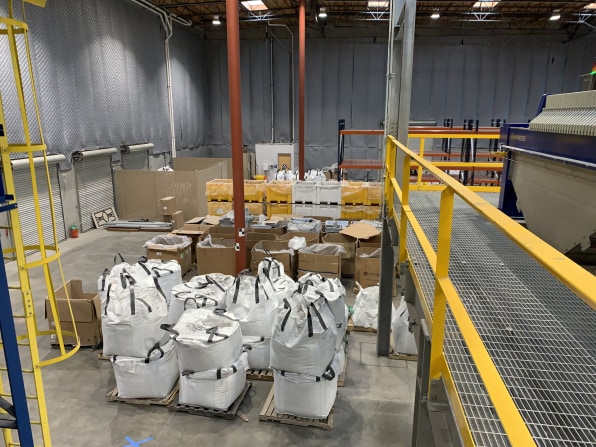
A sprawling new e-waste recycling facility near San Diego takes a different approach: The company, called Camston Wrather, doesn’t use heat, pressure, or chemicals. After it shreds the circuit boards to separate plastic from metal, it uses a proprietary “particle reduction” process to break down the materials mechanically. The result, which looks like sand, goes to a refiner. The company says its carbon footprint is around 90% lower than smelting. It also uses up to 95% less water than if it were mining materials from the ground.
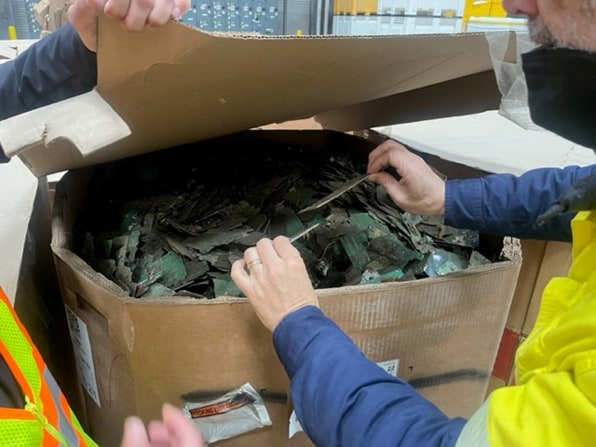
It’s a solution for one part of the massive problem of electronic waste. More than 50 million metric tons of it are generated globally each year, from computers and phones to smartwatches and TVs. In the U.S., where the average household has 24 electronic devices, e-waste is the fastest-growing waste stream. Another part of the problem comes from manufacturers not designing gadgets to be repaired, but rather continually pushing the shiniest new products at consumers.
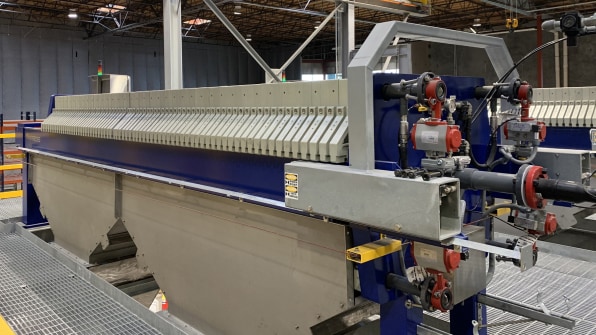
Most discarded gadgets aren’t recycled; only half of U.S. states have laws requiring e-waste recycling. Some electronics end up in landfills; others are forgotten in drawers. But even when devices are recycled, the recycling itself creates its own environmental challenges. (In the worst-case scenario, some e-waste is recycled in illegal scrapyards in Asia where workers burn imported trash and breathe in toxic fumes.) Camston Wrather wants to make recycling more sustainable.
As demand for precious metals keeps growing—for making everything from solar panels to EV batteries—recycling can help bolster supplies. The company says that it’s less expensive to get gold through its process than via traditional mining. In part, that’s because e-waste has such a high concentration of precious metals.
“Today, a financeable gold mine has 1 gram of gold per ton of ore,” says Dirk Wray, chairman and CEO of Camston Wrather. “E-waste has anywhere from 100 to 200 grams per tonne. And it’s rich with 22 metals.” While circuit boards are often shipped overseas for processing, the company wants to help build a shorter supply chain in the U.S. by working domestically.
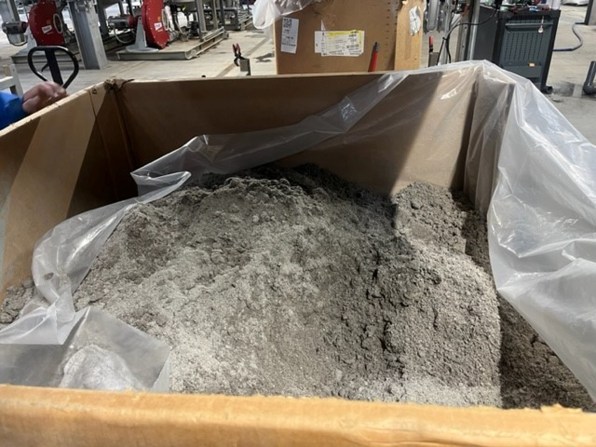
At six other locations around the country, the company breaks down old gadgets to take out materials like aluminum and plastic for recycling; then the circuit boards are sent to the new facility in Southern California. The plant can process 1.5 million pounds per month—still a tiny fraction of the flood of electronic waste that’s constantly being created. “You’d need about 500 of our plants to handle the problem globally,” Wray says.
The recycled metals are sold to manufacturers who want to avoid the environmental and social problems that come with traditional mining. Though the process is cheaper than mining, the green metals are sold at a premium; Camston Wrather is using the profits to quicken expansion. The second and third facilities that will use the new recycling technology are under development.
At a large scale, e-waste recycling could begin to replace some mines. “Would you be able to stop all mining?” Wray poses. “Probably not all mining, but a substantial amount.”