Tecnología de reciclaje URT para recicladores de baterías de litio
–Judith Wanjala– _ Celebrando otro contrato firmado en el stand de URT Recycling Technology durante la conferencia E-Waste en Frankfurt. De izquierda a derecha: Florian Hessler (URT), Michael Kedwesch (RE.LION.BAT Circular), Christoph Spandau (RE.LION.BAT Circular), Peter Hessler (URT), Thomas Deppe (RE.LION.BAT Circular GmbH) .
El reciclaje de baterías llegó para quedarse, insiste URT Umwelt- und Recyclingtechnik (Tecnología de reciclaje URT) de Alemania. Durante los últimos diez años, la compañía ha desarrollado una experiencia y un negocio sólido en la construcción de plantas de procesamiento de baterías de iones de litio que atienden a clientes de todo el mundo.
El reciclaje de baterías de iones de litio ha sido una parte esencial de la movilidad eléctrica desde el principio. La actividad se justifica por la chatarra de alta calidad que entrega importantes materiales valiosos necesarios para la producción de nuevas baterías.
URT Umwelt- und Recyclingtechnik de Alemania ha abordado el reciclaje de baterías de iones de litio de frente. El fabricante de plantas ha estado operando en el mercado de reciclaje más amplio durante 30 años y se estableció mediante la construcción de plantas para tratar chatarra de RAEE, en particular refrigeradores al final de su vida útil. Desde hace más de 10 años, desarrolla otra experiencia empresarial, la construcción de plantas para el reciclaje de baterías de iones de litio.
En el corazón de URT están Florian y Peter Hessler y Bernhard Biener. Peter Hessler es el md, el hijo Florian es un signatario autorizado y responsable de las ventas, mientras que Biener es el director técnico de la empresa.
CÓMO EMPEZÓ TODO: LITHOREC-2
En 2011, el trabajo comenzó con un emocionante proyecto llamado LithoRec-2. El objetivo principal era desarrollar procesos mecánicos, térmicos y químicos para el reciclaje de baterías de iones de litio. Junto con los socios Volkswagen y TU Braunschweig, URT participó y construyó una planta prototipo. Dentro de la planta, fue posible triturar células y paquetes de células y convertirlos en un estado homogéneo bajo una atmósfera de nitrógeno. Este procedimiento fue el punto de partida para todos los procesos posteriores: secado termomecánico, tratamiento hidrometalúrgico o tratamiento pirometalúrgico.
PLANTA PILOTO

El conocimiento obtenido de estos pasos de desarrollo es la base del concepto actual del fabricante de la planta. Durante esos primeros días, recuerda md Hessler de URT, no esperaba que LithoRec-2 se convirtiera en un segmento comercial completo. «Después de todo, en 2011 todos los fabricantes de equipos originales en Alemania se oponían a la electromovilidad», dice. “Sin embargo, URT ha desarrollado mucho el concepto y construyó una planta piloto en Volkswagen en Salzgitter en 2020. Este importante paso sirvió para recopilar más conocimientos. Como ejemplos, esto incluyó la resistencia de los materiales de sellado, el comportamiento del material a granel y el control de las purezas.’
98% RECUPERACIÓN
Con este conocimiento, URT construye desde 2021 plantas de reciclaje llave en mano a nivel industrial mediante tratamiento termomecánico. La ventaja de este tratamiento es la conservación del litio en la masa negra. Como resultado, las plantas URT pueden recuperar más del 98% de la masa negra seca. Gran parte del solvente liberado en el proceso también se condensa y se recupera.
La construcción de plantas industriales ha dado lugar a nuevos requisitos de rendimiento, seguridad operativa y automatización de plantas. Dependiendo de los requisitos de entrada y las pautas de emisión de los países individuales, las plantas siempre se construyen específicamente para el cliente. Por ejemplo, es posible duplicar el rendimiento de la planta más adelante.
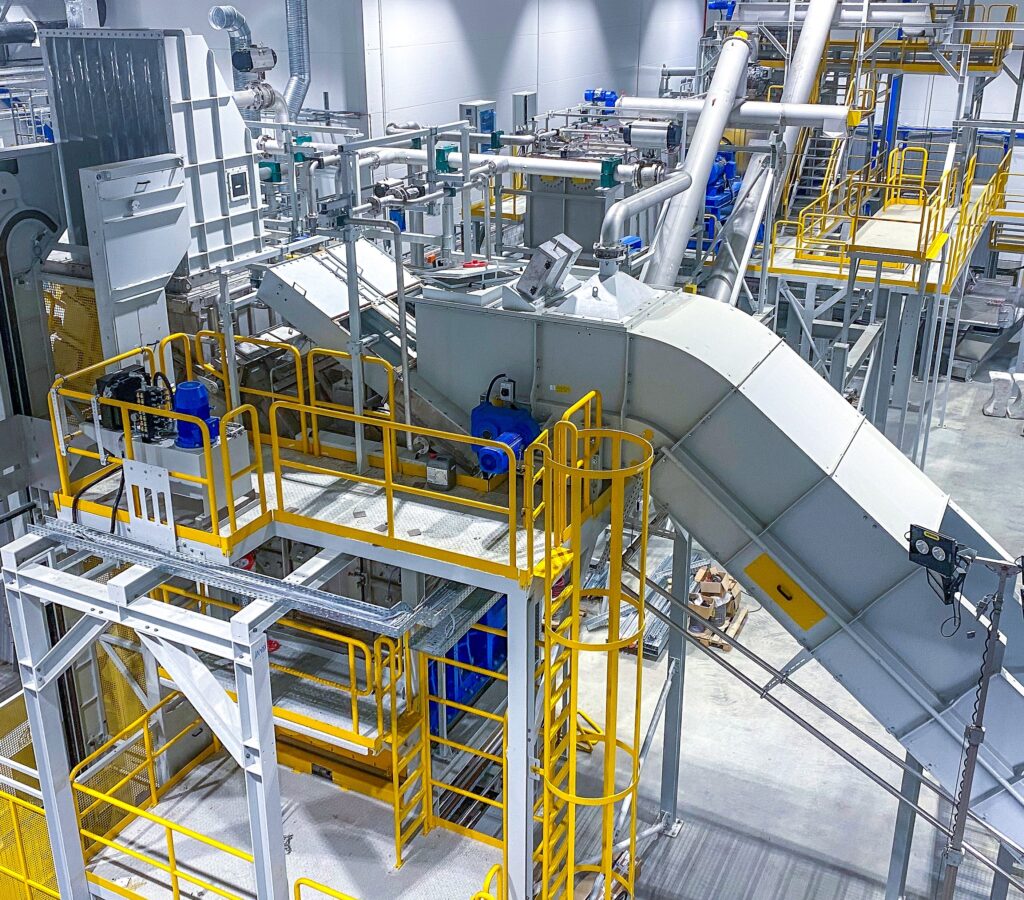
Aquí es esencial el conocimiento previo adquirido en la construcción de plantas de reciclaje de refrigeradores con respecto a la trituración inerte, la tecnología de esclusas de aire y cómo prevenir las emisiones difusas, particularmente la liberación de solventes de los electrolitos. «Estos están basados en hidrógeno, lo cual es congruente con los refrigeradores», agrega Hessler. ‘De esta manera, también se puede reutilizar el conocimiento sobre explosividad e inflamabilidad. Este es un factor decisivo para la planta y la seguridad operativa.’
A ESCALA INDUSTRIAL
La tecnología actual y los pasos del proceso incorporan este conocimiento. Comenzando con la trituración inerte en un solo paso, las baterías o partes de baterías previamente descargadas se transportan a través de la tecnología de compuertas a una trituradora inundada con nitrógeno, donde se trituran a un tamaño específico. Luego, el material de entrada se alimenta a través de sistemas de búnker a uno o más secadores de destilación al vacío, donde los solventes se evaporan de los electrolitos y luego se recolectan.
Aquí es esencial encontrar la temperatura, el tiempo de residencia y el vacío correctos para que coincidan con la entrada y la química de la celda. En el siguiente paso, todo el material de salida se enfría y luego ingresa a la primera máquina de cribado, lo que permite cribar una gran parte de la masa negra. Esta generación temprana da como resultado el 70-80% de la masa negra seca. El desafío aquí es recuperar la masa negra lo más pura posible, con pocas impurezas, como el aluminio de las carcasas o los materiales orgánicos y las películas. «El proceso de trituración es crucial aquí», subraya Hessler.